How the Best Cloud-Based Inventory Management Software Can Improve Your Supply Chain
A well-managed supply chain has never been more essential.
As supply chains become more complex and globalized, today's businesses face a daunting task: striking the right balance between efficiency, cost-effectiveness, and responsiveness to stay competitive. From managing suppliers to ensuring accurate inventory levels, a poorly managed supply chain can lead to delays, lost revenue, and dissatisfied customers.
That's where cloud-based inventory management software comes in, equipping businesses with real-time insights, automated processes, and better collaboration across the supply chain.
In this blog, we'll explain how the best cloud-based inventory management software can improve your supply chain and help you gain a competitive edge in a rapidly evolving market.
Let's get started.
Real-time data and visibility
Cloud-based inventory management software provides real-time data and visibility into inventory levels across the entire supply chain. While traditional, on-premise systems typically rely on manual updates or periodic data uploads, resulting in delays or inaccuracies, cloud-based solutions constantly sync inventory data, offering live updates on stock levels, shipments, and demand.
Real-time data enables businesses to make more informed decisions about inventory management. For example, if a surge in demand is detected, businesses can quickly adjust their orders to avoid stockouts. Conversely, if inventory levels are too high, they can cut back on orders to prevent overstocking, reducing the risk of obsolescence and wasted capital.
The ability to track and respond to real-time changes in the supply chain is particularly important for demand forecasting. Cloud-based systems provide a continuous data flow, helping businesses predict demand more accurately based on historical trends, seasonal fluctuations, and current market conditions. This level of insight means businesses can maintain optimal stock levels while making better pricing, marketing, and purchasing decisions.
Imagine a mid-sized electronics retailer struggling with frequent stockouts and overstock situations, leading to lost sales and wasted resources. After implementing a cloud-based inventory management system, the company gained real-time visibility into its supply chain. They could track inventory across multiple locations and forecast demand more accurately, leading to more accurate orders and satisfied customers. With real-time data, they could meet consumer demand more consistently, directly impacting their bottom line.
Better collaboration across the supply chain
Supply chain management often involves collaboration between multiple stakeholders, including suppliers, manufacturers, distributors, and retailers. Miscommunication or delays in sharing information can lead to costly errors and slow down the entire supply chain. This is where cloud-based inventory management software shines.
Cloud systems centralize inventory data in a single location, allowing all stakeholders to access the same information in real time. Whether it’s a supplier checking stock levels before shipping goods or a retailer verifying available products before placing an order, the cloud facilitates seamless communication and reduces the chance of misaligned expectations.
Centralized access to inventory data also helps coordinate supply chain activities, from planning production schedules to adjusting shipment dates based on current stock levels. This means businesses can respond faster to unexpected changes, reducing lead times and minimizing disruptions in the supply chain.
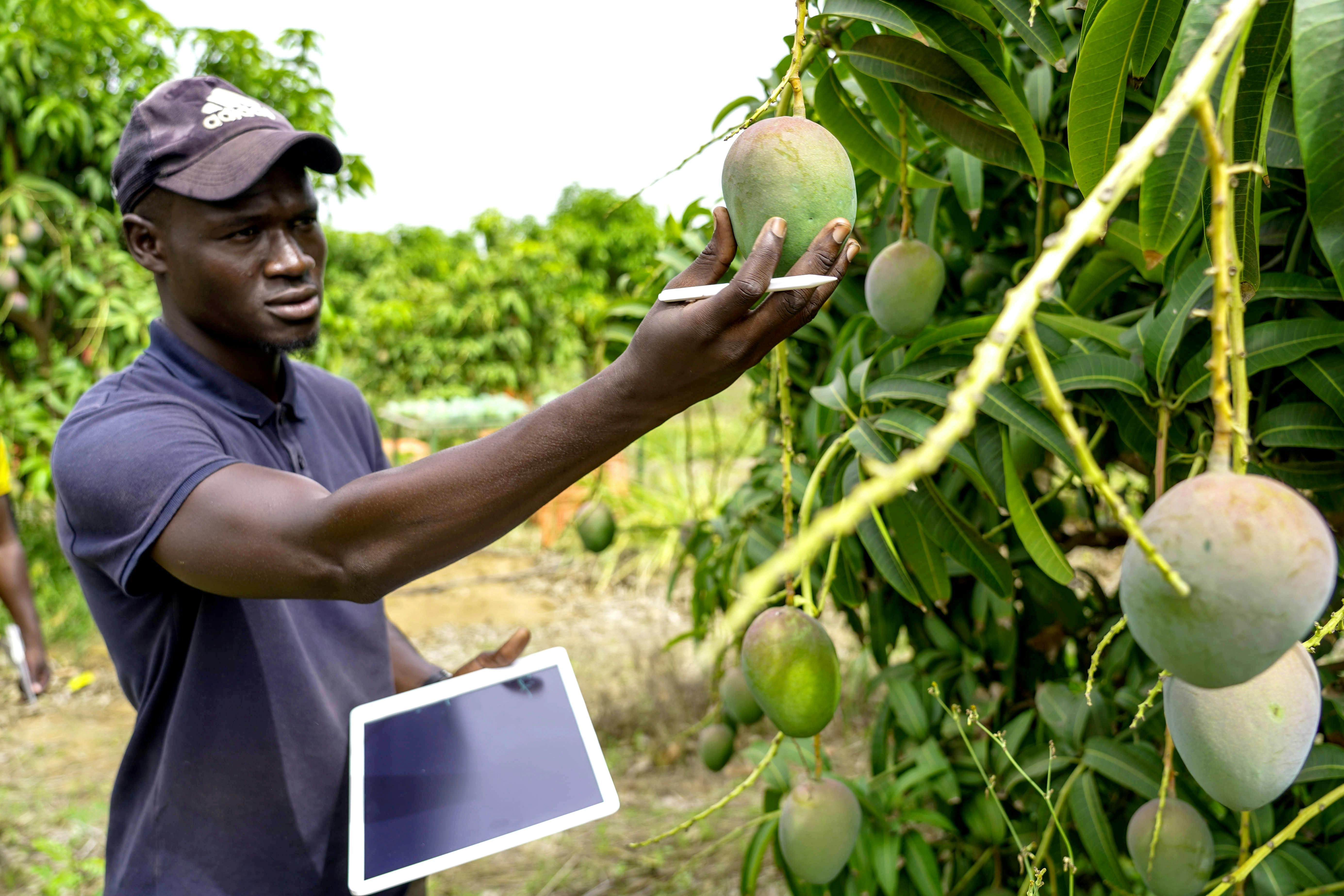
For example, a food and beverage manufacturer that works with multiple suppliers to source raw materials might find that delays in sharing stock information led to production halts. But, by implementing a cloud-based inventory management solution, the company could allow its suppliers and production teams to access real-time stock data. This would lead to better planning and reduced delays, helping the manufacturer meet customer demand consistently without disruptions.
More flexibility and scalability
In a world where markets and consumer demand can change in an instant, an adaptable supply chain is imperative. Cloud-based inventory management systems offer the flexibility and scalability necessary to respond to these changes without requiring significant capital investments or long lead times.
Unlike traditional systems that require costly hardware installations and manual updates, cloud-based inventory platforms are hosted online and can be scaled up or down based on business needs. Whether you're dealing with seasonal fluctuations, unexpected surges in demand, or expanding into new markets, a cloud solution can handle the increased complexity with ease.
This flexibility is especially beneficial for businesses with multiple locations or global supply chains. Cloud-based systems allow companies to manage their inventory from any location, facilitating growth without needing local servers or IT infrastructure. Moreover, cloud solutions often integrate with other business applications like accounting and CRM systems, streamlining operations and improving overall efficiency.
Picture a growing fashion retailer that started with a small brick-and-mortar shop before quickly expanding into e-commerce and multiple retail locations. As their business grew, so did the complexity of managing inventory across different locations. By adopting a cloud-based inventory management system, they could scale their operations seamlessly. The cloud platform provided the flexibility to add new locations and sales channels while maintaining accurate, real-time visibility into inventory levels across their supply chain.
Automated inventory replenishment
Replenishment is one of the most time-consuming and error-prone aspects of inventory management. Ensuring that stock levels are optimized without overstocking or running out of products is a delicate balancing act. Cloud-based inventory management software simplifies this process by automating inventory replenishment.
Automated replenishment systems use pre-set thresholds to trigger orders when stock falls below a specified level — a level of automation that reduces the need for manual inventory checks and minimizes the risk of human error. This means businesses can ensure that their shelves are always stocked with the right products, improving efficiency and reducing the risk of stockouts or excess inventory.
Automated replenishment systems can also optimize the timing and size of orders, helping businesses reduce lead times and improve relationships with suppliers. By streamlining the replenishment process, your organization can avoid costly delays and ensure it has the inventory you need to meet customer demand.
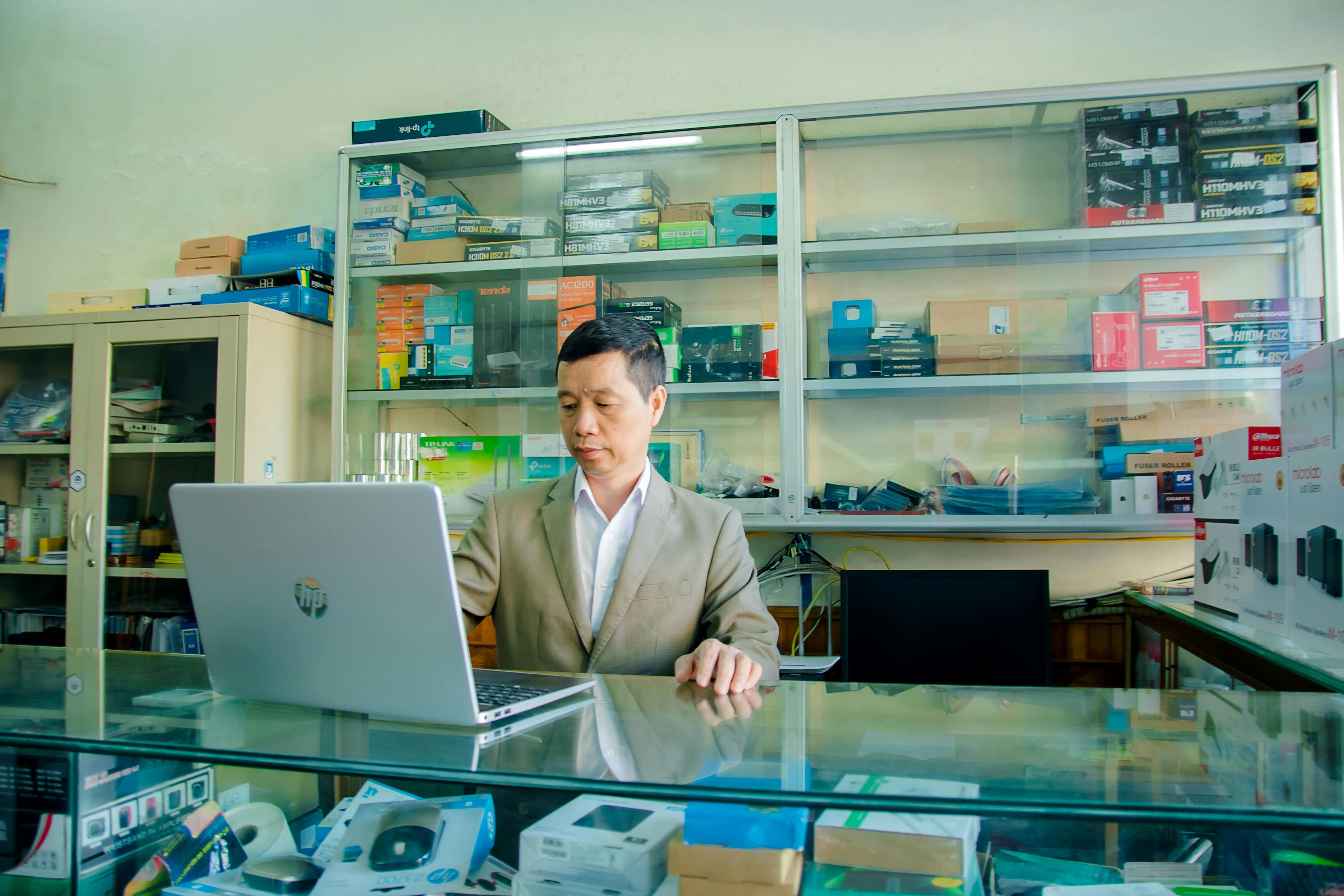
If a midsized electronics retailer experienced frequent stockouts, it would likely lead to lost sales and frustrated customers. But by implementing cloud-based automated inventory replenishment, the company could significantly reduce stockouts. The system could automatically place orders with suppliers when inventory levels dipped below a set threshold, ensuring that the retailer always had the right products in stock. Customer satisfaction would improve as a result, and the company would strengthen its relationships with key suppliers.
More efficiency, less risk
Cloud-based inventory management systems offer significant cost savings compared to traditional, on-premise systems. By eliminating the need for expensive hardware, server maintenance, and IT support, your business can reduce its upfront and ongoing operational costs. Cloud-based solutions typically operate on a subscription model, allowing companies to pay only for the features they need and quickly scale up as their business grows.
Another key benefit of cloud-based inventory management is risk reduction. By automating many aspects of inventory control — such as stock tracking, order processing, and demand forecasting — cloud systems help mitigate the risks of human error, stock discrepancies, and poor planning. The result is a more accurate, efficient, and resilient supply chain.
Take, for instance, a global distributor of consumer goods that implemented a cloud-based inventory management system to streamline its operations. By reducing manual data entry and automating inventory processes, the company could drastically cut warehousing costs and decrease stock discrepancies. Reducing errors and more accurate inventory control would help the business manage its supply chain risks — all while improving its profitability.
Tailor: Your ticket to a better supply chain
In today's highly competitive business environment, optimizing your supply chain is essential for success.
Cloud-based inventory management software offers numerous benefits that could improve your business's efficiency, visibility, and collaboration across the entire supply chain. By providing real-time data, automating critical processes, and offering the flexibility to scale as needed, cloud solutions are revolutionizing the way businesses manage their inventory.
Tailor's headless ERP solution can help your business unlock the full potential of cloud-based inventory management. With a powerful, flexible platform that integrates seamlessly with your supply chain, our cloud-based inventory solution ensures your business always operates at peak efficiency.
Ready to see how Tailor can transform your supply chain and drive your business forward?
Schedule your demo today.
Quick Answers and Frequently Asked Questions (FAQ)
What are the different types of inventory management?
Some of the most common inventory management methods are days sales of inventory (DSI), economic order quantity (EOQ), just-in-time management (JIT) and materials requirement planning (MRP). Other types include:
- ABC Analysis
- First-In, First-Out (FIFO)
- Last-in, first-out (LIFO)
- Safety Stock
- Weighted Average
- Specific Identification
- Perpetual Inventory System
- Periodic Inventory System
- Vendor-Managed Inventory (VMI)
- Consignment Inventory
Composable business systems and headless ERPs, like Tailor, empower businesses to dynamically adapt their inventory management strategy. By integrating modular components and real-time data, Tailor ensures seamless coordination across supply chains, reducing waste and optimizing stock levels. This flexibility allows businesses to implement the right inventory control method for their unique needs without being constrained by rigid ERP systems.
How can automation reduce inventory management errors?
Automated systems reduce human errors in data entry and order processing through smart reordering and demand forecasting, ensuring businesses maintain the right inventory levels.
With composable ERP systems, businesses can seamlessly integrate barcode scanning, RFID, and IoT sensors while leveraging smart automation to maintain optimal inventory levels.
Tailor's headless ERP allows businesses to adapt their inventory management strategy and blend these technologies with its flexible architecture — boosting efficiency, reducing errors, and enabling more scalable operations.
What is the role of scalability in inventory systems?
Scalability in inventory systems is crucial for businesses. It helps them grow and adapt to market changes while staying efficient.
Tailor's composable ERP solutions offer flexibility and easy integration — helping companies manage more work, expand operations, and maintain high service levels. At the same time, these solutions ensure cost-effectiveness and prepare businesses for the future. Using real-time data and AI-driven analytics, Tailor supports smarter inventory management and multi-channel integration, allowing businesses to scale easily and sustainably.