Manufacturing software, also known as software for manufacturing or production software, is a powerful tool that can revolutionize your operations. Over 54% of manufacturers intend to increase their investment in digital business software by at least 10%. By leveraging digital tools and applications, manufacturing software enables businesses to streamline processes, manage inventory, improve quality control, enhance production scheduling, and make data-driven decisions.
In this article, we will explore the different types of manufacturing software, delve into their key features and benefits, discuss how to choose the right software for your business, and provide strategies for successful implementation. We will also examine the future of manufacturing software in light of emerging trends and technologies.
Key Takeaways:
-
Manufacturing software streamlines processes, manages inventory, improves quality control, enhances production scheduling, and enables data-driven decision making.
-
Choose the right software by assessing your manufacturing needs, integrating with existing systems, considering customization and scalability, and ensuring vendor support and training.
-
Overcoming challenges such as technical issues, employee adoption and training, and data migration are crucial for successful implementation.
-
The future of manufacturing software includes trends in technology, the impact of AI and IoT, and the growing importance of sustainability and green practices.
Types of Manufacturing Software
The types of software commonly used in manufacturing include ERP systems, MES software, PLM software, SCM systems, and CAD/CAM software. Each type serves a specific purpose and addresses different areas of the manufacturing process. We will explore the features and benefits of each type of software and provide insights into their applications in the industry.
Below is a breakdown of each type of manufacturing software:
1. ERP (Enterprise Resource Planning) Software
ERP systems are comprehensive software solutions that integrate and automate various business processes across different departments. Manufacturing companies represent that largest group (47%) looking to purchase ERP software. Manufacturing ERP solutions help streamline operations by providing real-time visibility into production, inventory, sales, customer relationships, and finance. With ERP systems, manufacturers can optimize resource utilization, enhance collaboration, and improve decision-making.
-
Key Features:
-
Unified database for all business processes
-
Real-time data and analytics
-
Financial management and accounting
-
Customer relationship management (CRM)
-
Supply chain and inventory management
-
Human resources and payroll
-
Benefits:
-
Improved operational efficiency and productivity
-
Enhanced data accuracy and decision-making
-
Streamlined processes and reduced operational costs
-
Greater visibility across all departments
-
Improved customer satisfaction and service
2. MES (Manufacturing Execution Systems)
MES software focuses on the execution and control of the manufacturing processes on the shop floor. It provides real-time information on machine performance, production schedules, and quality metrics. MES systems enable manufacturers to monitor production activities, track inventory, ensure compliance with quality standards, and improve overall efficiency.
-
Key Features:
-
Real-time production monitoring and control
-
Detailed scheduling and dispatching
-
Quality management and compliance tracking
-
Machine performance and maintenance alerts
-
Material tracking and inventory management
-
Benefits:
-
Increased production efficiency and throughput
-
Reduced production costs and waste
-
Enhanced product quality and compliance
-
Improved responsiveness to production issues
-
Greater agility in responding to market demands
3. PLM (Product Lifecycle Management) Software
PLM software help companies manage the entire lifecycle of a product, from ideation and design to manufacturing, distribution, and end-of-life. It facilitates collaboration among design teams, suppliers, and stakeholders, ensuring seamless production planning and scheduling, product development and launch. PLM systems enable manufacturers to accelerate time-to-market, reduce manufacturing costs, and enhance product quality.
-
Key Features:
-
Product data management (PDM)
-
Collaboration tools for design and development teams
-
Bill of materials (BOM) management
-
Change and configuration management
-
Regulatory compliance and quality management
-
Benefits:
-
Accelerated product development and time-to-market
-
Reduced product development costs
-
Improved product quality and innovation
-
Enhanced collaboration across teams and departments
-
Effective management of product changes and updates
4. SCM (Supply Chain Management) Systems
SCM software is designed to manage the flow of materials, information, and resources across the supply chain. They help streamline procurement, production, and distribution processes, ensuring efficient inventory management, optimal supplier selection, and timely order fulfillment. SCM systems improve supply chain visibility, reduce lead times, and foster collaboration with suppliers and customers.
-
Key Features:
-
Supplier relationship management
-
Demand forecasting and planning
-
Inventory management and optimization
-
Logistics and transportation management
-
Order management and fulfillment
-
Benefits:
-
Enhanced supply chain visibility and coordination
-
Optimized inventory levels and reduced carrying costs
-
Improved supplier performance and relationships
-
Shortened lead times and faster order fulfillment
-
Increased customer satisfaction and loyalty
5. CAD/CAM (Computer-Aided Design/Manufacturing) Software
CAD/CAM software combines design and manufacturing capabilities to support the creation of products and their production processes. CAD tools enable manufacturers to create and modify product designs in a digital environment. CAM tools, on the other hand, generate toolpaths and instructions for the machines to manufacture the designed products. CAD/CAM software improves design accuracy, accelerates prototyping, and enhances manufacturing efficiency.
-
Key Features:
-
2D and 3D design and modeling capabilities
-
Simulation and analysis tools
-
Toolpath generation and CNC machine programming
-
Integration with PLM and ERP systems
-
Customizable design and manufacturing workflows
-
Benefits:
-
Improved design accuracy and efficiency
-
Reduced time and cost for prototyping and manufacturing
-
Enhanced product customization and complexity
-
Streamlined transition from design to production
-
Increased innovation and competitive advantage
Key Features of Manufacturing Software
In today's complex manufacturing landscape, implementing the right software can significantly improve business operations efficiency and productivity. Manufacturing software offers a range of key features that help businesses streamline their processes, optimize resource utilization, and drive success. In this section, we will explore the key features that manufacturing software provides, and how they contribute to efficient manufacturing operations.
Inventory Management
Effective manufacturing inventory management software is used by manufacturers to maintain optimal stock levels, minimize stockouts, and ensure timely order fulfillment. Manufacturing software offers robust inventory management capabilities, allowing businesses to track and monitor inventory levels, automate replenishment processes, and gain real-time visibility into stock movements. With features such as automated stock alerts, barcode scanning, and inventory optimization algorithms, manufacturers can improve inventory accuracy, reduce carrying costs, and enhance customer satisfaction.
Quality Control and Compliance
Quality control and compliance are paramount in manufacturing to ensure products meet established standards and regulatory requirements. Manufacturing software provides comprehensive quality management tools, enabling businesses to create and enforce quality control processes, track quality metrics, and conduct thorough inspections. From automating quality checks to capturing non-conformances and managing corrective actions, manufacturing software empowers companies to maintain product quality, comply with industry regulations, and mitigate quality-related risks.
Production Scheduling
Efficient production scheduling is essential for manufacturers to optimize resource utilization, minimize downtime, and meet customer demand. Manufacturing software offers advanced production scheduling features, allowing businesses to create optimal production plans, allocate resources efficiently, and manage production timelines. With real-time visibility into production schedules, manufacturers can identify potential bottlenecks, adjust schedules on the fly, and ensure smooth production flow. By optimizing production schedules, manufacturers can improve throughput, reduce lead times, and enhance on-time delivery performance.
Resource Allocation and Efficiency
Optimizing resource allocation is critical for manufacturers to maximize productivity and minimize costs. Manufacturing software provides resource management functionality, enabling businesses to effectively allocate labor, equipment, and materials based on demand and capacity. With features such as resource scheduling, capacity planning, and real-time resource tracking, manufacturers can optimize resource utilization, minimize idle time, and improve overall operational efficiency. By aligning resources with production requirements, manufacturers can eliminate bottlenecks, improve throughput, and achieve better bottom-line results.
Analytics and Reporting
Data-driven decision-making is a key driver of success in modern manufacturing. Manufacturing software offers robust analytics and reporting capabilities, allowing businesses to gain insights into their operations, monitor key performance indicators, and make informed decisions. With customizable dashboards, visualizations, and real-time reporting, manufacturers can analyze production data, identify trends, and uncover opportunities for improvement. By leveraging analytics and reporting features, manufacturers can optimize processes, drive continuous improvement, and stay ahead in a competitive market.
Benefits of Manufacturing Software
Implementing manufacturing software offers several benefits to businesses in the manufacturing industry. By utilizing the right software, companies can optimize their operations, enhance efficiency and productivity, improve product quality and compliance, streamline supply chain and inventory management, and make data-driven decisions.
Enhanced Efficiency and Productivity
Manufacturing software enables businesses to automate and streamline various tasks, reducing manual effort and saving time. This automation leads to enhanced efficiency and increased productivity as processes become more streamlined and less prone to errors. By automating repetitive tasks, employees can focus on more strategic and value-added activities, driving overall productivity improvements.
Improved Product Quality and Compliance
Manufacturing software offers robust quality control and compliance features that help businesses maintain high product standards and meet regulatory requirements. With real-time monitoring and automated quality checks, manufacturers can identify and address quality issues early in the production process, preventing costly rework and ensuring compliance with industry standards.
Streamlined Supply Chain and Inventory Management
Effective supply chain management is crucial for efficient manufacturing operations. Manufacturing software provides comprehensive tools for managing the supply chain, from procurement and inventory management to logistics and warehousing. By streamlining these processes, businesses can optimize inventory levels, reduce stockouts, improve order fulfillment, and enhance overall supply chain performance.
Data-Driven Decision Making
Manufacturing software generates vast amounts of data, allowing businesses to make data-driven decisions. With advanced analytics and reporting capabilities, manufacturers can gain valuable insights into their operations, identify trends, and predict future outcomes. This data-driven approach helps businesses make informed decisions, optimize resource allocation, and proactively address potential issues before they impact production.
Choosing the Right Software for Manufacturing Companies
When it comes to selecting the right manufacturing software, making the right choice is crucial for a successful implementation. Here are some key considerations to keep in mind:
Assessing Your Manufacturing Needs
The first step in choosing the right manufacturing software is to assess your specific needs. Determine the goals you want to achieve, such as improving production efficiency, streamlining inventory management, or enhancing quality control. Consider factors such as the size of your operation, the complexity of your manufacturing processes, and the specific requirements of your industry.
Integrating with Existing Systems
An important aspect to consider is how well the manufacturing software can integrate with your existing systems. Ensure that the software seamlessly integrates with your current ERP, CRM, and other business software to enable data sharing and eliminate silos. This integration is crucial for efficient information flow across departments and to avoid duplicate data entry.
Customization and Scalability
Choose manufacturing software that offers flexibility and customization options to align with your unique business needs. Look for a solution that allows you to configure workflows, add custom fields, and adapt the software to your specific processes. Additionally, consider the scalability of the software to ensure it can grow with your business as your manufacturing operations expand.
Vendor Support and Training
Vendor support and training play a vital role in the successful implementation of manufacturing software. Look for software vendors who provide comprehensive support, including technical assistance and regular software updates. Inquire about the availability of training programs and resources to ensure that your team can fully leverage the capabilities of the software.
Implementation Challenges and Solutions
Implementing manufacturing software can present various challenges that need to be addressed for a successful deployment. In this section, we will explore common implementation challenges, such as overcoming technical issues, ensuring employee adoption and training, and managing data migration and integration. We understand that these challenges can significantly impact the implementation process, but with careful planning and effective strategies, they can be mitigated to ensure a smooth transition to the new software.
Overcoming Technical Challenges
When implementing manufacturing software, businesses often encounter technical challenges that can hinder the adoption and effectiveness of the new system. These challenges may include compatibility issues with existing hardware and software, data security concerns, and system integration complexities. To overcome these challenges, it is essential to conduct a thorough evaluation of the existing IT infrastructure, perform compatibility tests, and establish robust security measures. Collaborating with experienced software providers and IT professionals can help identify and address technical challenges effectively.
Ensuring Employee Adoption and Training
One of the critical aspects of successful software implementation is ensuring employee adoption and training. Resistance to change, lack of understanding, and fear of job displacement can hinder the adoption process. To overcome these challenges, it is crucial to involve employees from the early stages of the implementation process. This can include providing clear communication and explanations about the benefits of the new software, conducting comprehensive training programs, and offering ongoing support. By involving employees and addressing their concerns, businesses can foster a positive mindset towards the new software and facilitate smooth adoption.
Managing Data Migration and Integration
Data migration and integration challenges are often encountered during the implementation of manufacturing software. Businesses need to ensure a seamless transfer of data from the existing systems to the new software without any loss or corruption. This requires careful planning, data cleansing, and mapping. Additionally, integrating the new software with existing systems, such as ERP or CRM, can present challenges in terms of data flow and synchronization. To overcome these challenges, it is essential to develop a robust data migration strategy, perform thorough testing, and collaborate closely with software providers and IT experts to ensure a smooth integration process.
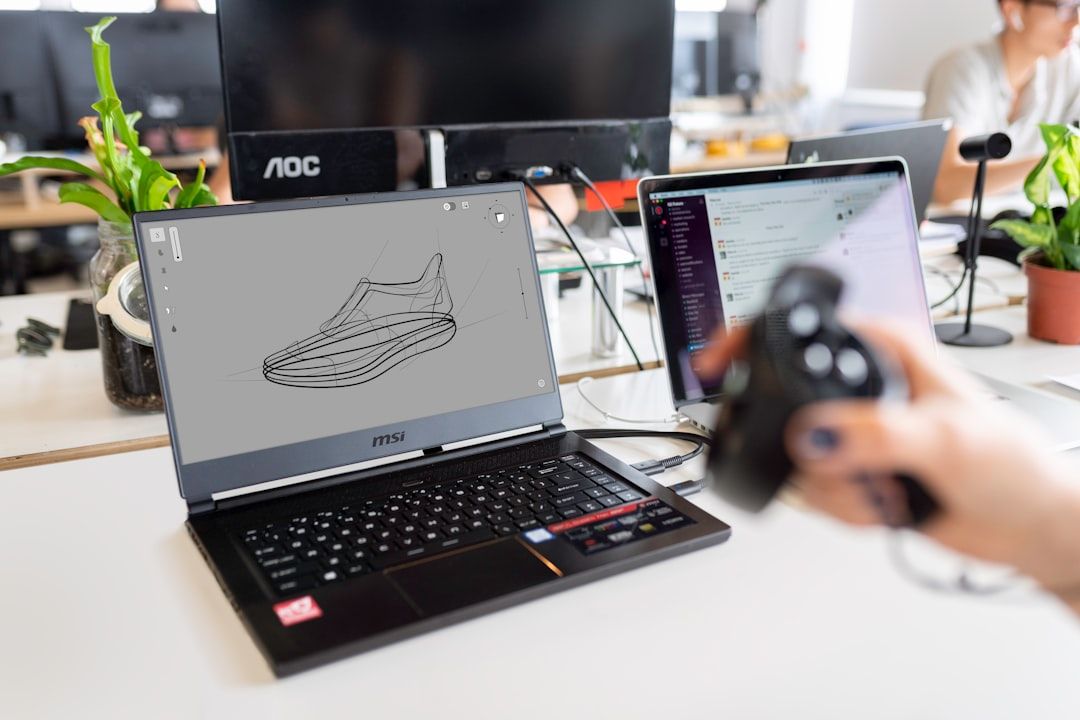
The Future of Manufacturing Software
This section highlights the evolving landscape of manufacturing software, driven by technological advances and a shift towards sustainability. We'll examine how AI, IoT, and green manufacturing are influencing the development of manufacturing software.
Key Technological Trends:
-
Automation and Robotics: Enhancing process efficiency and precision.
-
Cloud-Based Software: Offering scalable, real-time data access and collaboration.
-
Big Data and Analytics: Providing insights for optimized performance and decision-making.
-
AR and VR: Improving training, design, and simulation.
Impact of AI and IoT:
-
AI: Automates analysis and decision-making, boosting efficiency and reducing costs.
-
IoT: Connects devices for real-time monitoring, predictive maintenance, and improved inventory and supply chain management.
Sustainability in Manufacturing:
The push towards eco-friendly practices is reflected in software aimed at optimizing resource use and minimizing environmental impact. Key areas include:
-
Energy Efficiency: Software targets reduced energy consumption and waste.
-
Resource Management: Tools ensure materials, water, and energy are used efficiently.
-
Lifecycle Assessment: Analyzing environmental impact throughout a product's life.
As manufacturing continues to evolve, staying abreast of these trends and incorporating sustainable practices becomes crucial for future success.
Final Thoughts
Manufacturing software is a powerful tool that can significantly optimize operations in the manufacturing industry. By implementing the right software, businesses can enhance efficiency, improve product quality, streamline supply chain management, and make data-driven decisions.
When selecting a manufacturing software solution, it is essential to assess your specific needs and requirements. Consider factors such as seamless integration with existing systems, customization and scalability options, and the level of vendor support and training provided. By choosing the right software, you can ensure a smooth implementation process and maximize the benefits of the system.
Tailor provides customizable, scalable ERP solutions the assist modern manufacturing businesses. Request a demo today to see how Tailor can help your business to leverage advanced technologies and utilize an ERP system that evolves alongside your business.