Understanding ERP Maintenance Costs: What To Expect
The total cost of an ERP depends on the quality of the product and how well it's integrated into your business.
Like any complex, large-scale business solution, the initial purchase price isn't the whole story.
Unexpected costs are inevitable in business and technology. While rarely intentional, ERP maintenance can quietly creep up post-implementation (and create a noticeable increase as a budget line item). That's why it's necessary to understand the types of maintenance that may occur, how to control and account for them, and even how to minimize them.
Let’s break down the main categories of maintenance costs and strategies to manage them.
The Top 5 Components of ERP Maintenance Costs
It's easy to get hung up on the initial cost of an ERP: the product gets all the marketing and sales attention. The cost estimates may include estimates based on things that may or may not crop up — but a legacy ERP software provider knows that they'll be supporting your business for years to come and that the financial relationship between your businesses is fluid.
Because maintenance costs are different for every company, the overall long-term cost of an ERP implementation varies. While the ideal scenario for everyone is some simple software updates down the road, the complexity of tech stacks, aging hardware, and varying expertise levels of users often lead to inevitable additional costs.
Here are the top five costs we think you should keep in mind:
#1 — Subscriptions & Renewal Fees
ERP subscriptions come in various structures, from upfront yearly renewals to monthly or yearly charges. Plans can also vary with recurring fees based on usage or per-user charges — or sometimes a combination of all of these. As with all subscriptions, read the fine print and anticipate that rates may increase over time. Likewise, if your ERP charges per user, remember that each person you either hire or grant ERP system access will add additional recurring costs.
For some ERPs, the cost of additional users is baked in. However, the cost per additional user could be anywhere from a few dollars to $99+. Pricing-related costs for ERP products are ultimately dictated by your contract, so consider negotiating the details as your team grows and your business changes.
#2 — Product Updates
As with all software, ERPs require consistent updates and improvements. While some ERP providers include updates for a set period before charging for ongoing maintenance, others require separate fees for major updates. These updates aren’t just about adding new features: they often involve critical infrastructure changes that ensure security, compliance, and performance.
Additionally, highly customized ERP systems — especially legacy solutions — can make updates even more complex. The cost of upgrading may include consultation fees, debugging, data migrations, and even custom development from either the original provider or a third-party team. In some cases, outdated protocols or software dependencies can break integrations, requiring emergency fixes that further increase costs.
#3 — Training and Downtime
Speaking of updates, they can often introduce hidden costs beyond just the software and implementation fees themselves. Operational disruptions may occur as workflows adjust to new system changes, leading to temporary slowdowns or even internal reorganization. Training costs can also add up, as employees need to learn new features and updated processes, impacting productivity.
Most significant technology updates necessitate training and downtime. While it may be critical that your team has access to your ERP software at all times, implementation means that certain services may not be available immediately. Add in new functionality or unplanned outages, and the cost of an ERP can rise — especially if it's a legacy solution.
Training costs can come from hiring new employees or retraining current employees if workflows change. While not directly software-related, some training can be ongoing in the form of consulting as old workflows take time to unlearn and new workflows are not always adopted in practice as they were developed in theory. All this can slow your team down — and negatively impact productivity metrics like throughput and shipping times.
Downtime is an often unavoidable cost — whether you're experiencing an internet or server outage or your systems are undergoing maintenance.
#4 — Additional Customizations
Legacy ERP solutions are far more rigid than headless ERPs and often more restrictive when it comes to customization — meaning it's not uncommon for additional customizations to be expensive. While it may seem like a simple change to accommodate wholesale orders in your procurement workflow, these kinds of custom additions to a legacy ERP's functionality require development time, testing, and implementation windows that inevitably add to the cost.
A headless ERP might incur customization costs if you rely on outside development support. But because of their low-code nature, headless ERPs like Tailor are relatively easy to customize for in-house developers and contractors alike — enabling you to make high-impact changes and additions for a fraction of the cost.
Since the lead time for implementing new functionality in a headless system is usually a couple weeks (versus months), your business can more quickly react to the market opportunities that demand customization.
#5 — Tech Stack Integrations
Integrating new technology solutions — especially with a legacy ERP — will incur the cost of the license along with training and implementation. Much like customizations, this process can be both time and cost-intensive. Some tech stack additions will be cheaper than others, but with some legacy ERPs, integrations will require bespoke adjustments that inevitably incur greater technological debt later.
In contrast, headless ERPs are specifically designed to combat these costly issues.
By choosing API-powered software and services, integrating is as frictionless as possible — reducing development overhead and simplifying training. And by eliminating the need for bespoke solutions, keeping up with ERP system updates will be a breeze.
How to Control ERP Maintenance Expenses
Now that we’ve covered the most common ERP maintenance costs, here are strategies and tips for controlling how — and when — those costs hit.
-
Coordinate with your operational experts: Plan for your IT professionals and developers to partner closely with the operational roles in your organization. By ensuring that this group knows your ERP inside and out, they can advise on the best times to push updates and project timelines for additions to the software. By starting with the experts, you can better avoid miscommunications and stress caused by crunch. By giving them time to tinker with the work involved with updates and additions, the entire process can be streamlined and less costly.
-
Include department leaders in the conversation: One of the most complex parts of updating or adding to ERP software is adjusting the processes developed by different teams. Once the planning stages for updates or integrations begin, it's important to dialogue with company leadership to ensure they know what's coming so their teams are actively prepared.
-
Keep workflows and processes streamlined: Confused and (unnecessarily) complicated processes can be one of the primary drivers of increased ERP maintenance costs. If an update or addition hits the ERP system that impacts the viability of certain workflows, costs are generated from bottlenecks as teams scramble to adjust. When processes are streamlined and clear, they’re less likely to be impacted in a way that hurts your business’ bottom line.
-
Consider more frequent updates: An issue often seen with legacy ERP solutions is that a company will forgo minor updates to limit smaller periods of downtime or adjustment — making the major updates that much more difficult to implement. So, while it may be counterintuitive initially, planning for smaller updates and short periods of downtime can pay dividends later. Plus, getting your teams to anticipate these situations can help make your processes more efficient and flexible.
-
Prioritize automation: One of the greatest tools afforded to you by an ERP is being able to automate easily repeatable processes. When it comes to ERP maintenance costs, more automation in your workflows will lessen disruptive updates. Outside of updates, outages, or downtime, automation can offset costs by maximizing efficiency elsewhere.
In many cases, maintenance costs can’t be completely avoided. However, by leveraging timely communication, committing to optimizing workflows, and prioritizing the cost-saving power of automation, controlling the financial impact of maintenance is much easier.
Comparing Maintenance Costs Across ERP Systems
Now that we know how to control some of the typical ERP maintenance costs, it’s essential to compare costs between a headless ERP and legacy ERP solutions — while also accounting for general maintenance costs that could be incurred using either solution.
Legacy ERP solutions tend to be more expensive than headless ERP systems because they come as an all-in-one package. The overall size of the software is larger, requires more hardware integrations, and functions on proprietary codebases. Because of this, the maintenance costs can be exponentially higher; these costs usually scale in tandem with the size and profitability of your business.
Headless ERP solutions have much lower maintenance overhead because they decouple the UI and the backend, making it much easier to develop features. They also allow integration of the API-powered parts of your tech stack, reducing the need to purchase customizations. Adopting a SaaS (software as a service) model makes the hardware integration necessary to keep your ERP running much less demanding.
While both types of ERP solutions carry dramatically different maintenance costs, it’s also important to acknowledge that, like any software, they will be vulnerable to hardware issues, internet and intranet outages, software update implementations, and downtime due to new integrations, data backups, and security audits.
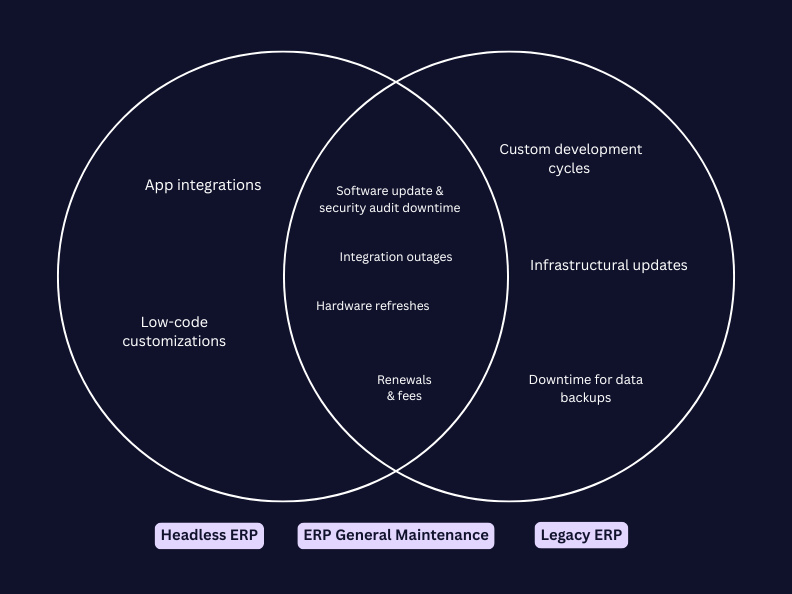
How to Make an Effective Budget for ERP Maintenance
When you’re considering signing a contract with your ERP service provider, keep these things in mind:
By incorporating these major maintenance costs into your ERP maintenance budget, you’ll have a much more accurate way to anticipate the recurring costs associated with ensuring your business remains scalable.
Strategies for Minimizing Unexpected ERP Maintenance Costs
While unexpected ERP maintenance costs are hard to predict, they can be minimized. These potential pitfalls should be prioritized and regularly included in quarterly and yearly business plans.
Assess Your Hardware
One of the more expensive unexpected costs is hardware failures. When internal servers fail or many company devices are impacted, the cost of new equipment and getting your systems back online is quite high. This is why it’s crucial to regularly assess the health of your people’s devices and your technology infrastructure. By keeping your equipment up-to-date and relatively current, you trade potential catastrophic failure for more regular expenditures.
Compile and Refine Your Processes
Another frequent area of maintenance cost comes from having messy processes that become incompatible with new technology integrations or customized ERP solutions. This particular cost comes from needing to completely retrain your people on processes along with technical debt related to antiquated tasking. In both cases, examine processes regularly, identify if optimizations can be made, and deploy tasking automation whenever appropriate.
Successfully automated tasks are less likely to be impacted by new integrations or additional module customizations.
Anticipate Future Needs
“Expect the unexpected” might sound cliché, but in reality, it’s about anticipating the unconsidered. Did a sudden supply chain disruption leave your team scrambling to adjust forecasts and meet customer demand? Or did an unexpected spike in ecommerce traffic expose gaps in your system's scalability? Planning ahead for these scenarios can save you from costly headaches when things don’t go as planned.
Maintenance expenses can also come from new integrations and customized modules. When these potential expenditures aren’t within the budget, they can quickly become large, unexpected costs.
Factor In Your Support Staff
Whether you contract a third-party IT team or have in-house technical staff, it’s paramount that they remain plugged into the ERP conversation. New hires must be trained to become functional experts, or your contracted teams should be fully aware of your current hardware, tech stack, and ERP solution. Having the right support staff can significantly minimize the impact of outages, service disruptions, or other unexpected events.
Evaluating ROI: Balancing ERP Investment and Maintenance Costs
Getting an accurate sense of the ROI of your ERP integration comes down to careful documentation. One way to do this is:
-
Take the total sticker price of your ERP implementation.
-
Tally up your recurring maintenance costs along with the funds you’ve set aside for unexpected costs.
-
Add this together and divide these total costs by how much revenue growth you brought in.
Over time, your ROI should increase steadily as your processes become more efficient and your profits increase. However, you don’t have to leave these ROI increases to chance.
Ways to improve ROI:
-
Utilize Automation: identify easily repeatable tasks and processes. By automating these within your ERP, you’ll instantly increase efficiency and productivity — reducing costs and increasing opportunities to increase revenue.
-
Leverage Predictive Analytics: by integrating an AI-driven ERP solution, you can receive reports that will help you identify customer behaviors and anticipate trends to capitalize on.
-
Minimize Procedural Waste: streamline your workflows, simplify your supply chain, and eliminate dated processes that lead to wasted time and energy. Even tasks that can’t be automated may benefit from optimization.
Last thoughts: ERP Maintenance & Security
While minimizing ERP maintenance costs is a worthwhile effort, there is one area we never recommend shortcutting: security.
With future costs of cybersecurity failures projected to eclipse $80 billion in 2026, it’s non-negotiable to prioritize security best practices in employee behavior and systems strength.
That’s why we recommend carefully evaluating all your tools (whether marketplace apps or larger platforms like an ERP or CRM) with industry standards. By ensuring your entire ERP solution can accommodate modern security measures, you can drastically minimize one of the most expensive business costs your business can face. The cost of a security breach could be catastrophic (IBM’s 2024 report estimates upwards of $4 million in damages). When it comes to ERP maintenance, your bottom line will thank you for keeping your teams trained, your software updated, and your budget prepared for regular ERP maintenance.